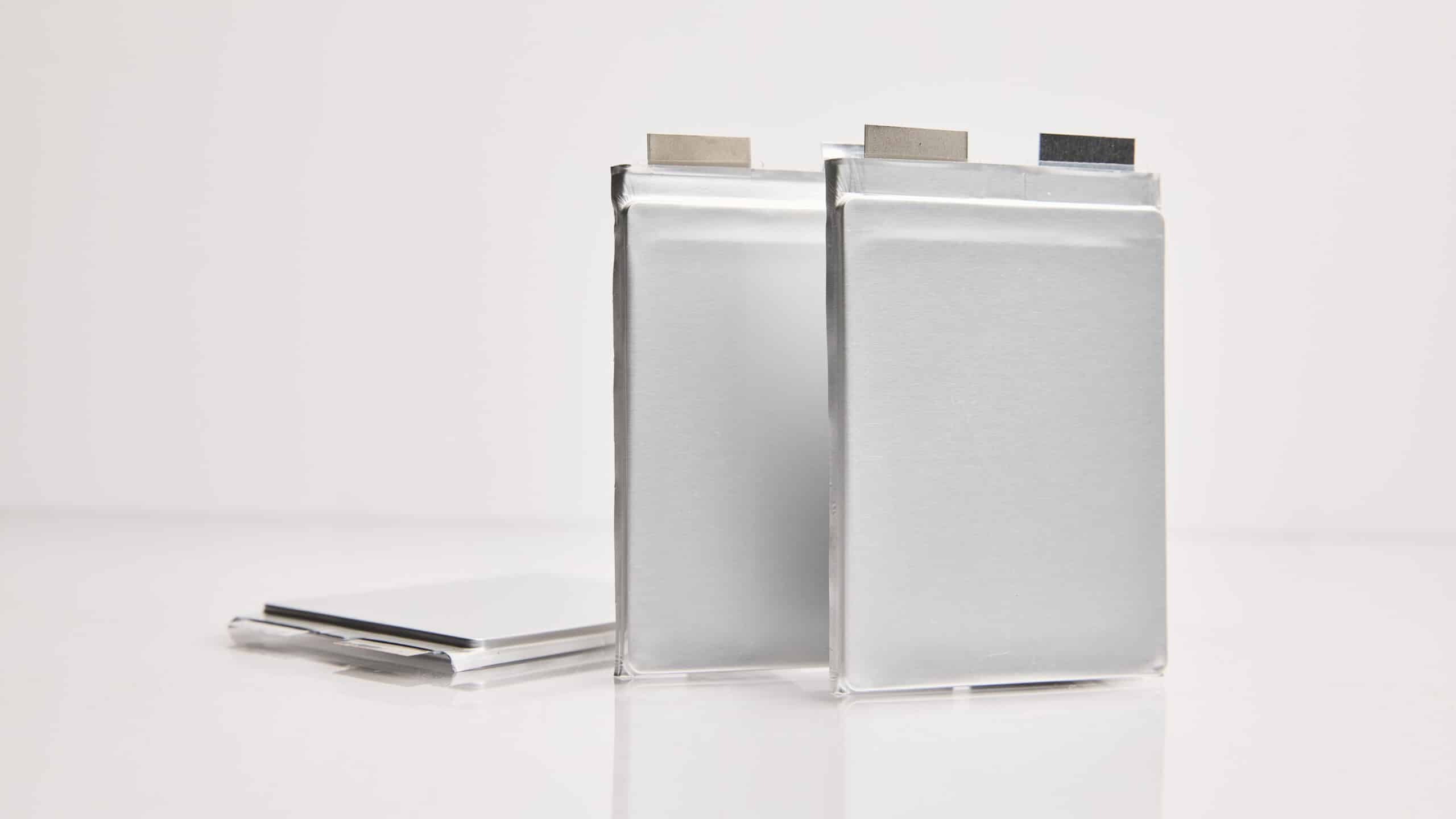
Our Strategic Blueprint
I took on the CEO role last year because I see QuantumScape as the global leader in solid state battery technologies with an ability to revolutionize energy storage and create tremendous shareholder value in the process.
In part 1, Understanding Battery Safety, we covered the basics of battery safety. In this blog article, we’ll look at battery safety testing and do a deep dive into a couple of key test results from energy-dense 24-layer QuantumScape prototype cells based on our Alpha-2 design.
A common way to evaluate battery safety tests is a grading system known as Hazard Levels. Each Hazard Level (HL) describes the behavior of a cell when subjected to a particular test – the higher the number, the more serious the safety risk: from HL0 (no reaction) to HL7 (an explosion). Many tests, such as nail penetration and cell crush tests, are destructive in nature, and so a result of HL 1 or below may not be possible in every case. For electric vehicle batteries, HL 4 or lower is typically considered a passing result, whereas HL 5 or above is nearly always considered failing.
Test Protocols
There are many sets of tests used to demonstrate battery safety in a variety of situations. A few common examples are:
Each of these standards requires a panel of different tests, but it’s worth looking at a few specific examples in more detail. Some examples of typical individual tests are:
It would be impractical to give an exhaustive list of all the variations of all the safety tests required by every safety protocol in every jurisdiction. However, there are two tests in particular that are worth examining in more detail: nail penetration and thermal stability.
It’s important to preface these results with a few caveats. First, these results are from prototype cells on the pathway to our QSE-5 design, not our final QSE-5 cells. Since product safety is a function of the precise cell design, the safety profile of the final cells may be different from these prototype cells. This is because safety is a function of cell materials and design, and consequently, when a given cell design changes, even slightly, the cell itself will have different physical characteristics and potentially a different safety profile. Any new cell design must therefore be re-tested to establish its behavior under abuse conditions.
Additionally, safety testing requires many types of tests using many individual cells to ensure statistically reliable conclusions about safety performance. Nevertheless, we believe the results presented here are a promising early indicator of the strength of our safety performance.
Nail Penetration
Nail penetration might be the most well-known battery safety test. It is certainly quite visually dramatic: In this test, the battery is punctured by a sharp metal spike to create an internal short-circuit. The purpose of this test is not necessarily to see whether the cell safely resists a puncture, since in the real world such an occurrence is unlikely (and highly inadvisable). Rather, the goal is to simulate how the battery might respond if an internal short were generated by a manufacturing defect, such as misalignment or metal fragment.
However, this test is not as straightforward as it may seem. The cell’s reaction depends heavily on precisely how the test is performed: factors such as speed and depth of penetration and the nail geometry can all significantly affect the result of the test. Counterintuitively, nail penetration does not always actually generate a short-circuit in the cell, and if a short isn’t created, then the nail penetration test does not test the consequences of an internal short-circuit at all. Nail penetration results cannot be interpreted without verifying that an internal short was created, by observing the characteristic voltage dip in concurrent electrical testing.
With this in mind, using energy-dense 24-layer prototype cells based on our Alpha-2 design, the QS performance on the nail penetration test shows that our solid-state lithium-metal system delivers good safety results under nail penetration testing. The nail penetration successfully induces an internal short-circuit inside the cell, but the cell does not enter thermal runaway, instead demonstrating only a modest temperature rise. The result is a Hazard Level of just 2, an excellent result for this type of test. We believe this good performance is attributable to the mechanical and thermal stability of our ceramic separator which, in contrast to conventional polymer separators, does not melt during the test.
Thermal Stability
The thermal stability test is straightforward: the cell is placed in a test chamber and heated up to simulate how the cell reacts to elevated external temperatures. This is the main mechanism by which EV battery packs experience catastrophic fire, as thermal runaway in one cell propagates to neighboring cells by heating them up until they experience thermal runaway themselves.
While the thermal stability test is straightforward, it is also very challenging for a battery to endure. Heating the cell directly tests the fundamental chemical stability of the materials in a way that translates to the real-world safety profile of an EV pack. We believe this test, better than any other, shows the limitations of liquid-based lithium-ion batteries and their fundamental susceptibility to thermal propagation. High-quality commercial battery cells, which pass many other safety tests with low hazard, can experience catastrophic failure when heated above a certain temperature. At 184 °C, the conventional lithium-ion battery cell we tested experiences a Hazard Level 6 failure: fire or flame with ignition and sustained combustion.
In contrast, using energy-dense 24-layer prototype cells based on our Alpha-2 design, QuantumScape’s solid-state technology demonstrates improved safety characteristics. When heated all the way to 300 °C, the QuantumScape battery passes with a result of Hazard Level 3: minor venting of gas from the liquid catholyte is the only significant effect.
We believe this demonstrates the fundamental safety advantage of our ceramic solid-state electrolyte-separator: because the ceramic is nonflammable and noncombustible, it essentially creates a series of firewalls as part of the electrochemical stack itself. With 24 of these ceramic sheets layered into each full cell, we expect that thermal runaway should be less likely compared to a conventional lithium-ion cell, which is flooded by a single contiguous mass of liquid fuel across all the layers of the cell.
Conclusion
As mentioned above, these early results are from prototype cells, not our final QSE-5 cells, and rigorous safety testing methodology requires a full suite of tests on many such cells before we can draw any firm conclusions about the safety performance of the finished product. Still, we’re encouraged that early prototype cell designs nevertheless display good safety performance.
From a big-picture perspective, a battery is by its very nature a highly reactive system that contains a lot of energy, and so there can be no such thing as a perfectly safe battery. However, we believe it is possible to improve the safety profile of conventional lithium-ion battery technology. At QuantumScape, we believe our ceramic solid-state electrolyte-separator has the potential to simultaneously offer both an improved safety profile and better energy, power, fast-charging, and cycle life, when compared with existing high-energy EV batteries. We also believe there is room to improve our safety profile even further, and we will continue to build, test, and refine our battery designs to achieve these improvements.
Forward-Looking Statements
This article contains forward-looking statements within the meaning of the federal securities laws and information based on management’s current expectations as of the date of this current report. All statements other than statements of historical fact contained in this article, including statements regarding the future development of QuantumScape’s battery technology, the anticipated benefits of QuantumScape’s technologies and the performance of its batteries, and plans and objectives for future operations, are forward-looking statements. When used in this current report, the words “may,” “will,” “estimate,” “pro forma,” “expect,” “plan,” “believe,” “potential,” “predict,” “target,” “should,” “would,” “could,” “continue,” “believe,” “project,” “intend,” “anticipates” the negative of such terms and other similar expressions are intended to identify forward-looking statements, although not all forward-looking statements contain such identifying words.
These forward-looking statements are based on management’s current expectations, assumptions, hopes, beliefs, intentions, and strategies regarding future events and are based on currently available information as to the outcome and timing of future events. These forward-looking statements involve significant risks and uncertainties that could cause the actual results to differ materially from the expected results. Many of these factors are outside QuantumScape’s control and are difficult to predict. QuantumScape cautions readers not to place undue reliance upon any forward-looking statements, which speak only as of the date made. Except as otherwise required by applicable law, QuantumScape disclaims any duty to update any forward-looking statements. Should underlying assumptions prove incorrect, actual results and projections could differ materially from those expressed in any forward-looking statements. Additional information concerning these and other factors that could materially affect QuantumScape’s actual results can be found in QuantumScape’s periodic filings with the SEC. QuantumScape’s SEC filings are available publicly on the SEC’s website at www.sec.gov.
I took on the CEO role last year because I see QuantumScape as the global leader in solid state battery technologies with an ability to revolutionize energy storage and create tremendous shareholder value in the process.
QuantumScape’s planned first commercial product, QSE-5, is a ~5 amp-hour cell designed to meet the requirements of automotive applications. Here, we’ll walk through the various elements of the cell specifications and explain some of the complexities behind the seemingly simple metric of energy density.
I took on the CEO role last year because I see QuantumScape as the global leader in solid state battery technologies with an ability to revolutionize energy storage and create tremendous shareholder value in the process.
QuantumScape’s planned first commercial product, QSE-5, is a ~5 amp-hour cell designed to meet the requirements of automotive applications. Here, we’ll walk through the various elements of the cell specifications and explain some of the complexities behind the seemingly simple metric of energy density.
Privacy Policy | Terms of Use
© 2025 QuantumScape Battery, Inc.
1730 Technology Drive, San Jose, CA 95110
info@quantumscape.com
Pamela Fong is QuantumScape’s Chief of Human Resources Operations, leading people strategy and operations, including talent acquisition, organizational development and employee engagement. Prior to joining the company, Ms. Fong served as the Vice President of Global Human Resources at PDF Solutions (NASDAQ: PDFS), a semiconductor SAAS company. Before that, she served in several HR leadership roles at Foxconn Interconnect Technology, Inc., a multinational electronics manufacturer, and NUMMI, an automotive manufacturing joint venture between Toyota and General Motors. Ms. Fong holds a B.S. in Business Administration from U.C. Berkeley and a M.S. in Management from Stanford Graduate School of Business.