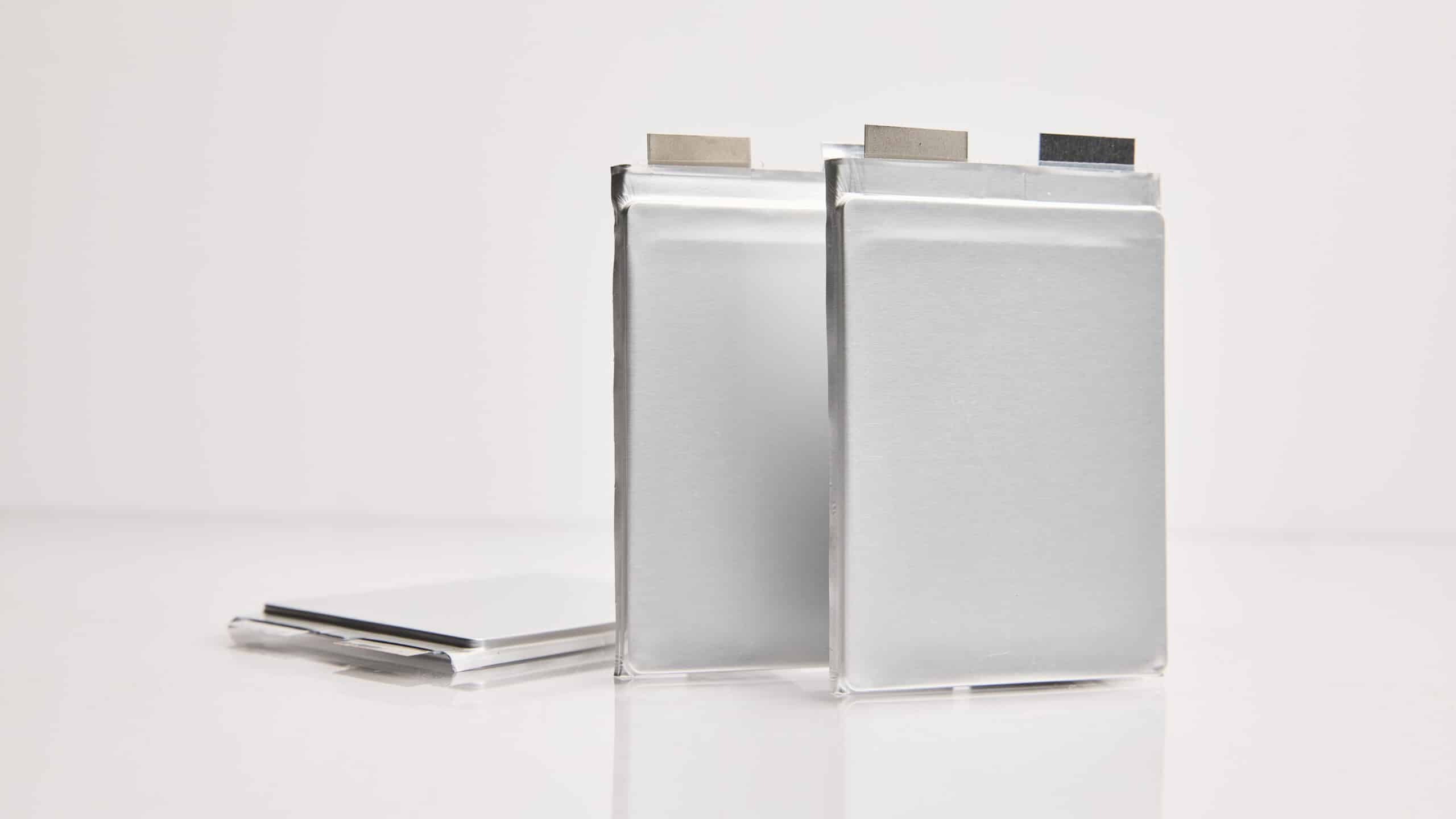
Our Strategic Blueprint
I took on the CEO role last year because I see QuantumScape as the global leader in solid state battery technologies with an ability to revolutionize energy storage and create tremendous shareholder value in the process.
QuantumScape’s solid-state lithium-metal battery technology is designed to deliver disruptive improvements to electric vehicle performance. However, lithium metal poses some unique challenges that require innovations in cell architecture to address. Our answer to these challenges is a new cell format, FlexFrame.
FlexFrame is a cross between a conventional pouch cell and a prismatic cell and is intended to enable a technological step-change improvement through elegant simplicity of design.
There are two fundamental features of the FlexFrame architecture: a frame that wraps around the edge of the cell stack, and a flexible outer layer of polymer laminate, which is similar to conventional pouch cell material.
When manufactured, the cell is anode-free, and the cell stack is in its most contracted position, with the face of the cell sitting around a millimeter below the frame. As the cell charges and the anodes of each layer are plated with pure lithium metal, the cell face is pushed out, along with the flexible packaging material. When fully charged, the face of the cell is designed to be almost totally flush with the frame.
In addition to accommodating expansion and contraction, FlexFrame is designed to allow the cell to simultaneously:
Temperature
All batteries generate a certain amount of heat during operation, and higher rates of power typically result in more heat. This means that to enable vehicles with quick acceleration and fast charging, you need a battery management system that can quickly pull heat out of the individual battery cells to keep them at their optimal operating temperature. In this context, a high-performance battery cell needs not only good fundamental chemistry, but also intelligent cell design, to enable good thermal performance.
Conventional cell designs all manage heat in more or less the same way: as the cell heats up during operation, the thermal energy must move from the layers of the cell to the external casing, where the pack cooling system draws it away. However, a lithium-metal cell format must expand and contract, and it is difficult to engineer a mechanism, such as a spring or foam, which will both move flexibly and conduct heat effectively from the cell face.
To address this challenge, the FlexFrame design splits these tasks in two. While the exterior face of the cell can expand and contract as necessary, the heat generated can be transferred directly from the individual cell layers to the exterior frame, which can then be cooled from the back or sides. We’re currently working with our partners to develop and validate thermal management systems incorporating our FlexFrame cell design.
Pressure
FlexFrame is designed to work with or without external pressure. If required, pressure can be applied to the external face of the cell, and because heat can be transferred out to the sides of the frame, it’s possible to apply pressure externally while cooling the cell at the same time. However, we have shown data from single-layer cells that demonstrate our lithium-metal platform can deliver long cycle life with zero externally applied pressure, and FlexFrame is intended to be able to operate under these conditions as well.
Manufacturing and pack integration
As a hybrid of conventional prismatic and pouch designs, FlexFrame allows us to leverage tools and materials that are already used in the battery industry. The exterior polymer laminate material is similar to what is found in conventional lithium-ion pouch cells, and the frame gives the cell good mechanical stability, which is provided at the module level for a conventional pouch cell. When assembling the cell, we can use conventional stacking and sealing techniques, which will aid in high-volume manufacturing. And unlike cylindrical cells, FlexFrame cells can fit neatly next to one another with minimal wasted volume, enabling improved overall pack energy density relative to a cylindrical cell format.
Energy density
As discussed in a previous blog, energy density at the cell level is not just about chemistry; packaging also plays an important role. One goal of any cell format is to minimize the amount of dead weight and wasted volume taken up by the inactive materials, such as the cell casing, and maximize the proportion of the cell’s active materials, the part of the cell that actually stores energy. Optimizing this packaging efficiency is key to enabling high cell-level energy density.
FlexFrame has been designed with this important consideration in mind. Because the lightweight pouch cell material and the low-profile frame add minimal overhead to the cell, we project our new cell format is capable of delivering energy density above 800 Wh/L in QSE-5, our planned 5 amp-hour cell, with significant room for improvement in a higher-capacity design.
We believe solid-state lithium-metal batteries are the future of electric transportation, and the FlexFrame architecture represents our vision for that future. First and foremost, it addresses the unique challenge of lithium-metal expansion, which any lithium-metal system will have to solve. In addition, we believe its elegant design is capable of good thermal performance and efficient packing at the module level, while allowing for high cell-level energy density. And importantly, it’s designed to allow for rapid mass manufacturing using materials and processes similar to those used at scale in today’s battery industry.
At QuantumScape, our goal has always been to transform electric vehicle batteries, and we believe FlexFrame is a step toward bringing this technology to real-world EVs.
Forward-Looking Statements
This article contains forward-looking statements within the meaning of the federal securities laws and information based on management’s current expectations as of the date of this current report. All statements other than statements of historical fact contained in this article, including statements regarding the future development of QuantumScape’s battery technology, the anticipated benefits of QuantumScape’s technologies and the performance of its batteries, and plans and objectives for future operations, are forward-looking statements. When used in this current report, the words “may,” “will,” “estimate,” “pro forma,” “expect,” “plan,” “believe,” “potential,” “predict,” “target,” “should,” “would,” “could,” “continue,” “believe,” “project,” “intend,” “anticipates” the negative of such terms and other similar expressions are intended to identify forward-looking statements, although not all forward-looking statements contain such identifying words.
These forward-looking statements are based on management’s current expectations, assumptions, hopes, beliefs, intentions, and strategies regarding future events and are based on currently available information as to the outcome and timing of future events. These forward-looking statements involve significant risks and uncertainties that could cause the actual results to differ materially from the expected results. Many of these factors are outside QuantumScape’s control and are difficult to predict. QuantumScape cautions readers not to place undue reliance upon any forward-looking statements, which speak only as of the date made. Except as otherwise required by applicable law, QuantumScape disclaims any duty to update any forward-looking statements. Should underlying assumptions prove incorrect, actual results and projections could differ materially from those expressed in any forward-looking statements. Additional information concerning these and other factors that could materially affect QuantumScape’s actual results can be found in QuantumScape’s periodic filings with the SEC. QuantumScape’s SEC filings are available publicly on the SEC’s website at www.sec.gov.
I took on the CEO role last year because I see QuantumScape as the global leader in solid state battery technologies with an ability to revolutionize energy storage and create tremendous shareholder value in the process.
QuantumScape’s planned first commercial product, QSE-5, is a ~5 amp-hour cell designed to meet the requirements of automotive applications. Here, we’ll walk through the various elements of the cell specifications and explain some of the complexities behind the seemingly simple metric of energy density.
I took on the CEO role last year because I see QuantumScape as the global leader in solid state battery technologies with an ability to revolutionize energy storage and create tremendous shareholder value in the process.
QuantumScape’s planned first commercial product, QSE-5, is a ~5 amp-hour cell designed to meet the requirements of automotive applications. Here, we’ll walk through the various elements of the cell specifications and explain some of the complexities behind the seemingly simple metric of energy density.
Privacy Policy | Terms of Use
© 2025 QuantumScape Battery, Inc.
1730 Technology Drive, San Jose, CA 95110
info@quantumscape.com
Pamela Fong is QuantumScape’s Chief of Human Resources Operations, leading people strategy and operations, including talent acquisition, organizational development and employee engagement. Prior to joining the company, Ms. Fong served as the Vice President of Global Human Resources at PDF Solutions (NASDAQ: PDFS), a semiconductor SAAS company. Before that, she served in several HR leadership roles at Foxconn Interconnect Technology, Inc., a multinational electronics manufacturer, and NUMMI, an automotive manufacturing joint venture between Toyota and General Motors. Ms. Fong holds a B.S. in Business Administration from U.C. Berkeley and a M.S. in Management from Stanford Graduate School of Business.