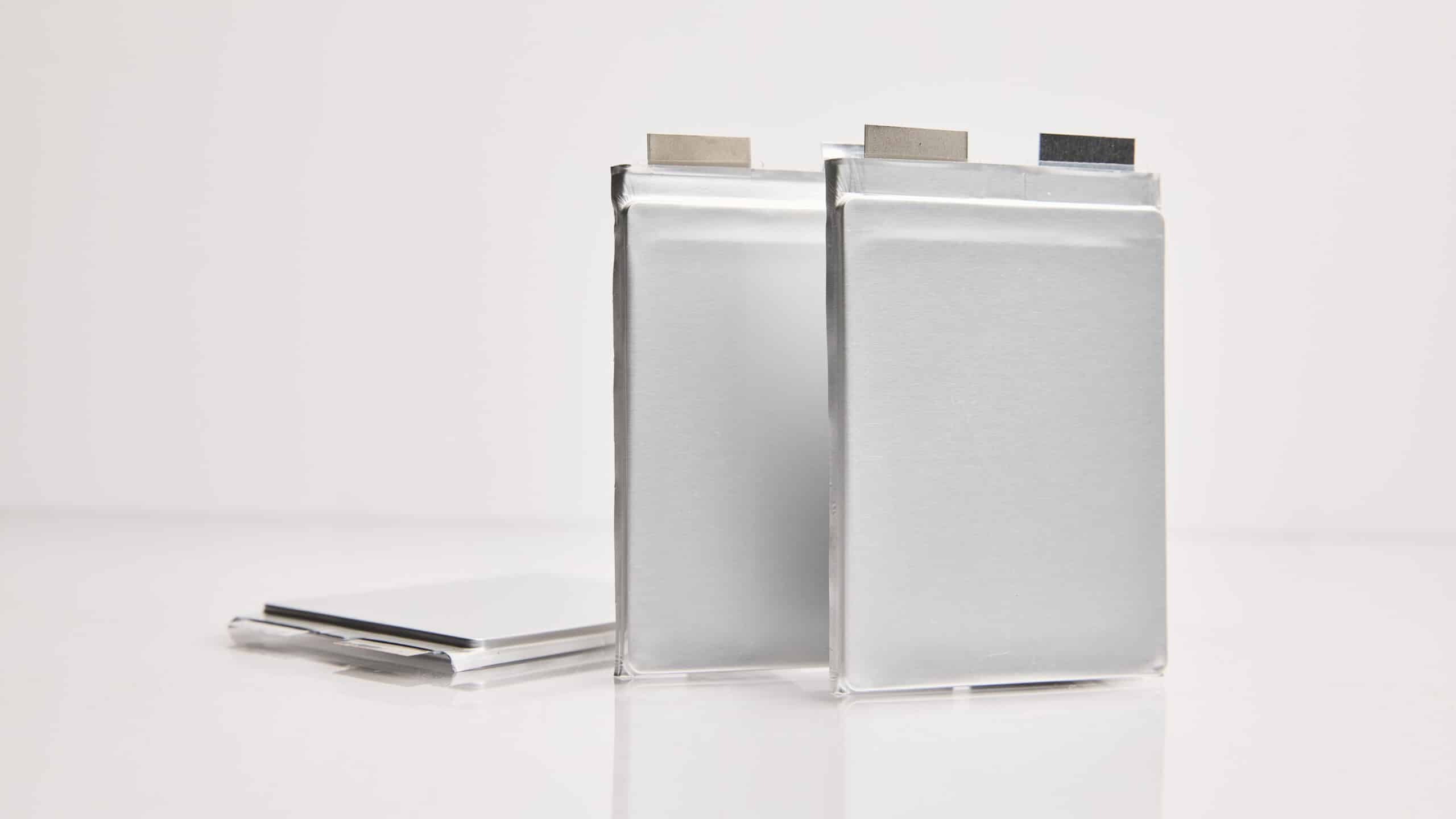
Our Strategic Blueprint
I took on the CEO role last year because I see QuantumScape as the global leader in solid state battery technologies with an ability to revolutionize energy storage and create tremendous shareholder value in the process.
Today’s electric vehicle battery market is characterized by various technologies and chemistries, addressing different user requirements. Some automotive models target customers who prioritize a long driving range; for these drivers, there are more energy-dense batteries based on nickel manganese cobalt (NMC) or nickel cobalt aluminum (NCA) cathodes. Although cell-level costs of these chemistries have decreased substantially over the past decade, they still sit on the higher end of the spectrum, with recent estimates putting them at around $100 per kilowatt-hour (kWh).
Other models focus on customers who want the lowest-cost option. For these drivers, today’s most common option is a battery based on lithium iron phosphate (LFP) cathodes; the cell-level cost of LFP-based batteries is roughly 20% lower than NMC or NCA, around $80 per kWh. In addition to lower costs, these batteries offer several other advantages over those based on NMC or NCA, including higher thermal stability and better cycle life. Unfortunately, these benefits come at the expense of lower energy density, which reduces driving range.
At QuantumScape, we believe both high and low energy density battery chemistries need to improve. Today’s high energy density NMC chemistries are still too expensive and don’t offer performance competitive with existing combustion-engine vehicles. Low-cost LFP-based chemistries are too low in energy density for wide-scale market adoption. And both battery types still use graphite or graphite/silicon anodes that impose manufacturing costs and performance limitations on the cell.
So what can QuantumScape’s solid-state lithium-metal technology contribute to the continued performance increases and cost declines that will drive mass adoption of electric vehicles? It’s best to think of our solid-state lithium-metal battery as a technology platform that can take advantage of many streams of innovation over the coming years. We believe replacing the conventional graphite anode in lithium-ion batteries with a pure lithium-metal anode is the most effective pathway to increase the energy density of EV batteries and address other key limitations, such as charge time.
The data we shared in our Battery Showcase came from cells built with an NMC cathode, which has very appealing characteristics for high-end, high-performance vehicles. However, other cathode technologies, such as LFP, are being deployed in other segments of the automotive industry. Although LFP is increasingly popular in medium-cost, lower-range vehicles, it has some fundamental drawbacks that have limited its use in mainstream EVs. The advantage of our solid-state lithium-metal platform is that it can both improve on LFP’s strengths and substantially reduce its weaknesses.
Like many inventions that have made the lithium-ion battery possible, LFP cathode material was discovered in the lab of Nobel-laureate Professor John Goodenough.[1] Unlike other common oxide cathode materials, LFP is a polyanion compound; that is, it’s composed of more than one negatively charged element (oxygen and phosphorus). Its atoms are arranged in a crystalline structure called olivine, which forms a 3D network for intercalation of lithium ions; this is in contrast to the 2D slabs that form layered oxides like NMC and NCA.
The main challenge of working with LFP cathode material was the poor transport of electrons and lithium ions through the polyanionic olivine structure. This poor transport contributed to high cell resistance and limited power performance. However, reducing the size of LFP particles to nanoscale and the addition of carbon coatings around the particles have significantly improved LFP’s power performance, to the point that it’s now often used in power cells.[2]
LFP has several advantages over other popular cathode chemistries:
LFP is widely known for its low cost, with some estimates putting it as much as 70% lower per kilogram than nickel-rich NMC. The cost advantage comes from its chemical composition – iron and phosphorus, two earth-abundant elements that are mined at enormous scales across the globe and are widely used in many industries. In contrast, NMC cathodes contain nickel and cobalt, which are scarcer and, in the case of cobalt, mined under controversial conditions. And although nickel-rich NMC replaces most of the cobalt with nickel, nickel is still orders of magnitude less abundant than iron (0.0084% vs 5.63% of the earth’s crust[3]) and its global production volume is hundreds of times less than iron.
LFP is very thermally stable, which means it takes higher temperatures to decompose and burn.[4] In the event of thermal runaway, LFP releases one-sixth of the heat of nickel-rich NMC. This means that cooling and safety systems in the battery pack can be simplified without sacrificing safety, thus providing additional cost savings and decreasing the risk of expensive battery recalls in the case of manufacturing defects.
With this enhanced safety, battery packs can be constructed with more densely packed cells (e.g., cell-to-pack architecture), increasing the effective energy density. In commercial EV battery packs based on NMC and NCA, cells account for 40% or less of total pack volume, whereas the most advanced LFP cells can achieve 60% pack volume utilization.
LFP often offers better cycle life compared to NMC.[5] One reason for this is its lower operating voltage; given the high-voltage instability of common liquid electrolytes, LFP cells are less prone to side reactions that reduce capacity and increase cell resistance. Another reason is that LFP cathodes are more structurally and chemically stable than NMC cathodes, so they can withstand more cycles without breaking apart and losing their ability to store lithium ions. LFP batteries could conceivably power a car for over a million miles.
All of these characteristics make LFP one of the more cost-effective solutions available for EV batteries, and its market share has grown substantially over the past few years.
However, LFP has a critical disadvantage: low energy density. There are two primary causes for this. First, compared to nickel-rich NMC, LFP has a lower capacity[6]; that is, it can’t store as many lithium atoms per unit mass and per unit volume. And second, LFP has a lower operating voltage than NMC. Since the energy available in a battery is a product of capacity times voltage, an LFP cell of a given cathode thickness stores less energy than a higher-voltage NMC cell. These factors explain why LFP cells generally have lower energy densities than nickel-rich NMC cells: 350-450 Wh/L vs. 700 Wh/L, respectively. Although manufacturing and engineering innovations have made LFP-based battery packs somewhat more energy dense, there is still a wide gap between LFP and more expensive alternatives like NMC.
Poor energy density directly impacts the value of LFP in various applications. The low volumetric energy density (the amount of energy stored in a given volume) limits the battery capacity that can physically fit into a typical automotive drivetrain, putting an upper limit on vehicle range. And the low gravimetric energy density (the amount of energy that can be stored per unit of mass) means an LFP-powered EV battery pack will be heavier than an equivalent NMC pack, impairing acceleration and handling and requiring tougher shock absorbers and sturdier brakes. LFP has been very popular in electric buses, since they have plenty of room to store bulky batteries, stay within a few dozen miles of their charging hubs, and don’t need to accelerate rapidly. In contrast, personal passenger vehicles are a more challenging use case. The reduced energy density means that EV battery packs based on LFP rarely exceed total energies of 60 kWh, in contrast to the >80 kWh battery packs based on NMC and NCA that power high-end, long-range EVs.
This energy density problem is not easily addressed at the cell level. For example, one way to increase the energy density of a battery cell is to add silicon to the anode, and some next-gen battery technologies are relying on this. But silicon also has a substantial voltage penalty relative to graphite. In an LFP cell, which is already at relatively low voltage, this additional reduction in voltage compromises part of the energy density gains achieved through the higher capacity of the silicon anode. In addition, advanced silicon-rich anode materials are expensive to produce, so making a silicon anode would increase LFP cell costs substantially, which undermines its most persuasive selling point. In short, we don’t believe silicon anodes are the solution to the LFP energy density problem.
We consider QuantumScape’s solid-state lithium-metal technology to be cathode agnostic for a couple of reasons:
In a typical lithium-ion battery with a liquid electrolyte, the anode and cathode are in chemical communication through the liquid, and thus a change to one electrode may cause unexpected or unwanted behavior in the other. This means every part of the cell must be engineered to cooperate with every other part. In a sense, every new battery chemistry must be completely bespoke, and this development process is expensive, time consuming, and rife with unexpected challenges. In contrast, QuantumScape’s lithium-metal anode and solid-state separator technology platform can take advantage of a variety of different cathodes with few changes to the platform itself, while still improving energy density and lowering cost.
For example, LFP cells built on the QuantumScape platform could achieve energy densities between 600-700 Wh/L and ~250 Wh/kg, roughly 50% better than current LFP cells. This would put them almost on par with today’s best NMC-based cells. And unlike silicon, pure lithium metal enjoys a slight voltage advantage over graphite, adding a small boost to cell energy. The QuantumScape platform could thus cut the weight of a 50 kWh LFP battery pack by more than 100 pounds.
This would already represent substantial progress toward bringing LFP to the mainstream. But we believe the most exciting part is that the QuantumScape platform offers the potential to reduce the cost of these superior LFP cells relative to their conventional counterparts. Low-cost LFP cathodes mean the graphite anode material makes up a larger percentage of the overall cell cost; some estimates put anode material at roughly 20% of the entire cost of an LFP cell.[7] In contrast, the QuantumScape platform is a fundamentally different approach to cell design: our cell does away with the anode host material, pulling the lithium from the cathode as the battery charges and storing it as a pure metal in the anode. Consequently, eliminating the material and processing costs associated with anode manufacturing and formation presents an opportunity for a QuantumScape LFP cell to drive costs down substantially.
It’s important to emphasize that these cost and performance advantages stack on top of any future improvements that might be made to the LFP cathode, such as dry electrode processing. And the technology platform that will enable this won’t need to be re-engineered from the ground up to incorporate these breakthroughs. When we achieve full manufacturing scale, we expect our platform to be the most cost-efficient and energy-dense pathway for a wide variety of cathode chemistries in mass-market lithium-based batteries.
In the Q2 2021 shareholder letter, we showed test results of our solid-state lithium-metal platform with an LFP cathode. The coin-sized cells showed excellent compatibility after 100 cycles under our standard test conditions, demonstrating the versatility of our platform with different cathode materials.
We are currently partnering with world-class suppliers of LFP cathode material and plan to offer both NMC- and LFP-based cathodes to our automotive OEM partners. Our OEMs can choose the cathode type best suited for each of their models while enjoying improved energy density, charge times, and economics over conventional graphite- or silicon-based anodes.
Our goal is to bring to market a solid-state lithium-metal battery platform that, when matched with the right cathode, can serve a diverse variety of applications, from the high-end to the everyday. Electrifying the 95% of the automotive market that has yet to adopt EVs requires improvements to both performance and cost. Our platform offers the rare opportunity to do both, simultaneously.
Lithium-based rechargeable batteries have not reached their full potential. In the coming decade, we expect new developments in cathode technology to further improve cost and performance. Our contribution to this constant stream of innovation is a platform that can offer these new technologies the most energy-dense and lowest-cost anode configuration possible. Our platform offers the chance to accelerate the transition to clean, renewable energy while raising the bar on what consumers can expect from batteries.
[1] https://iopscience.iop.org/article/10.1149/1.1837571/meta
[2] https://pubs.acs.org/doi/10.1021/acsenergylett.1c00743
[3] Abundance of elements in the earth’s crust and in the sea, CRC Handbook of Chemistry and Physics, 97th edition (2016–2017), p. 14-17
[4] http://ecec.me.psu.edu/Pubs/2021_Yang_NatureEnergy.pdf
[5] https://iopscience.iop.org/article/10.1149/1945-7111/abae37
[6] https://www.sciencedirect.com/science/article/pii/S1369702114004118
Forward-Looking Statements
This article contains forward-looking statements within the meaning of the federal securities laws and information based on management’s current expectations as of the date of this current report. All statements other than statements of historical fact contained in this article, including statements regarding the future development of QuantumScape’s battery technology, the anticipated benefits of QuantumScape’s technologies and the performance of its batteries, and plans and objectives for future operations, are forward-looking statements. When used in this current report, the words “may,” “will,” “estimate,” “pro forma,” “expect,” “plan,” “believe,” “potential,” “predict,” “target,” “should,” “would,” “could,” “continue,” “believe,” “project,” “intend,” “anticipates” the negative of such terms and other similar expressions are intended to identify forward-looking statements, although not all forward-looking statements contain such identifying words.
These forward-looking statements are based on management’s current expectations, assumptions, hopes, beliefs, intentions, and strategies regarding future events and are based on currently available information as to the outcome and timing of future events. These forward-looking statements involve significant risks and uncertainties that could cause the actual results to differ materially from the expected results. Many of these factors are outside QuantumScape’s control and are difficult to predict. QuantumScape cautions readers not to place undue reliance upon any forward-looking statements, which speak only as of the date made. Except as otherwise required by applicable law, QuantumScape disclaims any duty to update any forward-looking statements. Should underlying assumptions prove incorrect, actual results and projections could differ materially from those expressed in any forward-looking statements. Additional information concerning these and other factors that could materially affect QuantumScape’s actual results can be found in QuantumScape’s periodic filings with the SEC. QuantumScape’s SEC filings are available publicly on the SEC’s website at www.sec.gov.
I took on the CEO role last year because I see QuantumScape as the global leader in solid state battery technologies with an ability to revolutionize energy storage and create tremendous shareholder value in the process.
QuantumScape’s planned first commercial product, QSE-5, is a ~5 amp-hour cell designed to meet the requirements of automotive applications. Here, we’ll walk through the various elements of the cell specifications and explain some of the complexities behind the seemingly simple metric of energy density.
I took on the CEO role last year because I see QuantumScape as the global leader in solid state battery technologies with an ability to revolutionize energy storage and create tremendous shareholder value in the process.
QuantumScape’s planned first commercial product, QSE-5, is a ~5 amp-hour cell designed to meet the requirements of automotive applications. Here, we’ll walk through the various elements of the cell specifications and explain some of the complexities behind the seemingly simple metric of energy density.
Privacy Policy | Terms of Use
© 2025 QuantumScape Battery, Inc.
1730 Technology Drive, San Jose, CA 95110
info@quantumscape.com
Pamela Fong is QuantumScape’s Chief of Human Resources Operations, leading people strategy and operations, including talent acquisition, organizational development and employee engagement. Prior to joining the company, Ms. Fong served as the Vice President of Global Human Resources at PDF Solutions (NASDAQ: PDFS), a semiconductor SAAS company. Before that, she served in several HR leadership roles at Foxconn Interconnect Technology, Inc., a multinational electronics manufacturer, and NUMMI, an automotive manufacturing joint venture between Toyota and General Motors. Ms. Fong holds a B.S. in Business Administration from U.C. Berkeley and a M.S. in Management from Stanford Graduate School of Business.